Building a Future-Proof Manufacturing Operation: The Essential Steps
By Richard Winsor on June 24, 2024
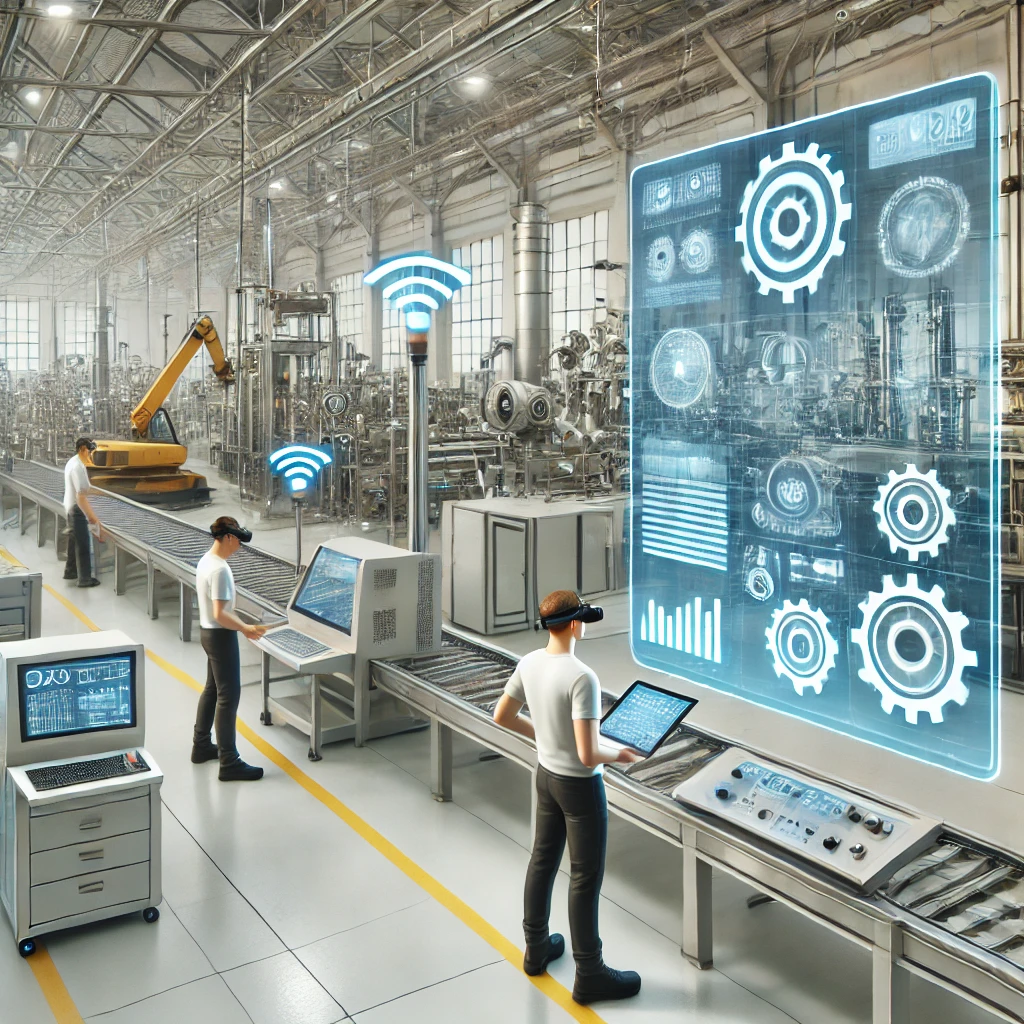
Digital transformation is more than just technology; it’s about laying the right foundations first. Discover how a balanced approach can lead to unparalleled operational success.
Introduction
In today’s fast-evolving manufacturing landscape, digital transformation promises to revolutionize operations. Picture a future where production lines run seamlessly without human oversight, achieving remarkable accuracy and efficiency. While this vision seems futuristic, the key to realizing it lies in foundational work.
Lessons from the Automotive Industry
Historically, the automotive industry has set precedents with initiatives like General Motors’ 1980s “factory of the future.” Despite not achieving full automation, the foundational technologies and processes they implemented still influence modern manufacturing.
Challenges and Solutions
A significant challenge today is that while 58% of manufacturing leaders pursue autonomous plant initiatives, many struggle with basic data tracking and staff retention. Technology alone isn’t the solution; it acts as an accelerator. The crucial first step is to establish robust operational foundations—understanding asset failures, refining workflows, and aligning organizational goals.
Strategic Questions for Manufacturers
For a successful digital transformation, manufacturers must balance people, processes, tools, and technology. It’s essential to start with a clear understanding of what changes are needed and why. Too often, companies invest heavily in IT systems without clarifying their purposes, leading to failures.
Ask yourself: What are your organization’s goals? How automated do you need to be? How critical is data collection for your operations? Addressing these questions helps create a focused strategy.
Tools and Integration
Using tools like application rationalization and data capability assessment can aid this process. Ensuring these tools are effectively integrated into workflows is equally vital. Transitioning from reactive to proactive operations depends on this balance.
Optimizing Workforce with Technology
The labor shortage has highlighted the need for optimized processes and better workflow management. Capturing the expertise of experienced workers through digital means, such as augmented reality and electronic work instructions, is crucial. Technology not only replaces retiring employees but also upskills the current workforce.
Risk-Based Asset Management
With foundational work in place, and initial technology deployments enhancing operations, it’s time to consider a risk-based asset management plan. This involves mapping value streams, analyzing machinery data, and understanding the impact of equipment failure on business processes.
For instance, a global pharmaceutical company leveraged AI and machine learning to predict equipment failures, developing comprehensive user requirements for their asset performance management (APM) platform. This strategic deployment phase underscores the importance of ongoing digital transformation.
Continuous Improvement
Ultimately, better reliability and maintenance practices lead to financial stability and improved worker retention. Digital transformation is an ongoing journey requiring continuous innovation and adaptation. By investing in people and laying the right foundations, manufacturers can turn “lights-out” operations into a tangible reality.
#Innovation #Management #Technology #Strategy #DigitalTransformation #Manufacturing #SmartOperations #Automation #AI #MachineLearning
For more information, visit 2KR Partners.
Related Articles: Fix Your Operations First, Then Technology Can Shine